1, sliding line blanking
Cut the ingot to a reasonable size and weight according to product requirements;
2. Heating (including tempering)
The heating equipment is mainly single-chamber furnace, push-rod furnace and table annealing furnace, all heating furnaces use natural gas as fuel, the heating temperature of the ingot is generally 1150℃~1240℃, the heating time of the cold ingot is about 1~5 hours, the heating time of the hot ingot is half of the heating time of the cold ingot, and the heated ingot enters the forging process.
3. Forging
When the ingot is heated to about 1150~1240℃, it is removed from the heating furnace, and then put into an air hammer or an electric hammer by the operator. According to the size of the ingot and the forging ratio requirements, the corresponding pier thickness and drawing length are carried out. The forging size is monitored in real time, and the forging temperature is controlled by an infrared thermometer.
4. Inspection
The preliminary inspection of the forging blank is mainly the inspection of appearance and size. In terms of appearance, the main inspection is whether there are cracks and other defects, and the size must ensure that the blank margin is within the scope of the drawing requirements, and make a good record.
5. Heat treatment
A comprehensive process in which the forging is heated to a predetermined temperature, held for a certain time, and then cooled at a predetermined speed to improve the internal organization and performance of the forging. Its purpose is to eliminate internal stress, prevent deformation during machining, and adjust the hardness to make the forging conducive to cutting. After heat treatment of the ingot, according to the requirements of the material of the ingot air cooling or water cooling, quenching treatment.
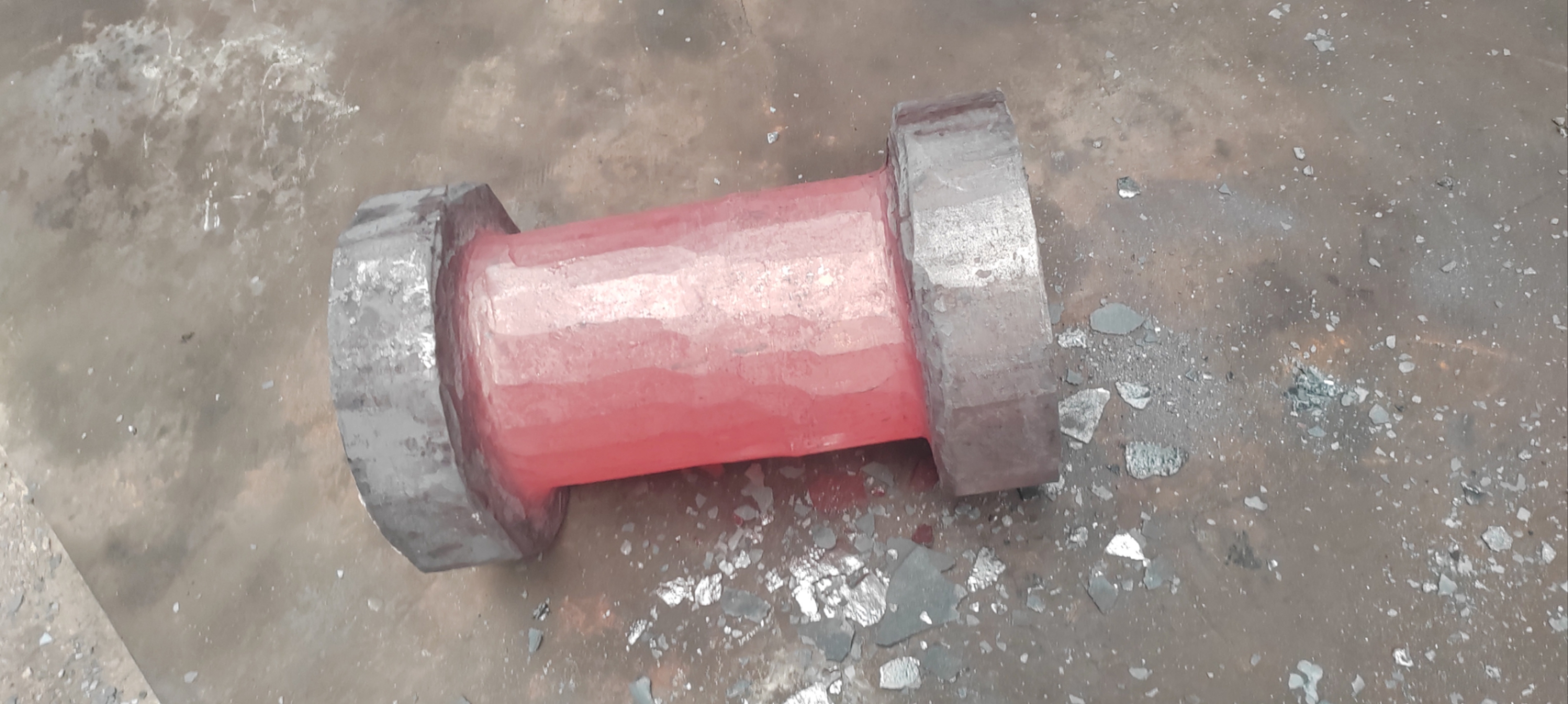