The problem of choosing the die forging step is both complex and flexible. The following is based on the process characteristics of various forgings to explain the rule of choosing the die forging step and the problems that should be paid attention to under normal circumstances.
Cake satins are also called short shaft forgings. Its characteristic is that the billet is upset along the axis and the horizontal projection of the forging is uniform and symmetrical. When choosing the die forging step, it can be divided into three cases according to its forming difficulty: ordinary forging, high hub deep hole forging and high rib-thin wall complex forging.
The working steps of common forgings are upsetting, upsetting and final forging. This kind of forgings such as gear, flange, 10 axis, etc., the shape is relatively simple.
Bar forgings are also called long shaft forgings. It is characterized that the blank axis is perpendicular to the striking direction of the forging hammer, and the metal is distributed along the blank axis and formed into the forging. When choosing the work step, according to the forming characteristics of the forging is divided into: short forging, straight long shaft forging, forging with branches, forging with fork, forging with Gongyu shaped section and bending axis forging and other six cases.
When the cross section of the forging does not change much along the axis and the length of the blank is similar to the length of the forging, the working steps are: flattening, final forging, pressing shoulder or clamping, final forging. When the cross section of forging does not change much, it adopts the flattening working step, which can remove the oxide skin. After flattening, the blank will be rotated 90° around the axis to set the final forging with a narrow edge.
When the forging is flat and wide, the blank press fan is translated into the final forging. For forgings with large cross-section changes, the shoulder step can also be used. Due to the large width of the concave part of the forging, and in order to make the blank after pressing the shoulder easy to position and swing in the final forging die chamber, the blank does not turn over after pressing the shoulder, and the final forging is translated. The purpose of upsetting is to smooth out the surface, avoid folding, and remove the oxide skin. An iron upsetting quantity is small.
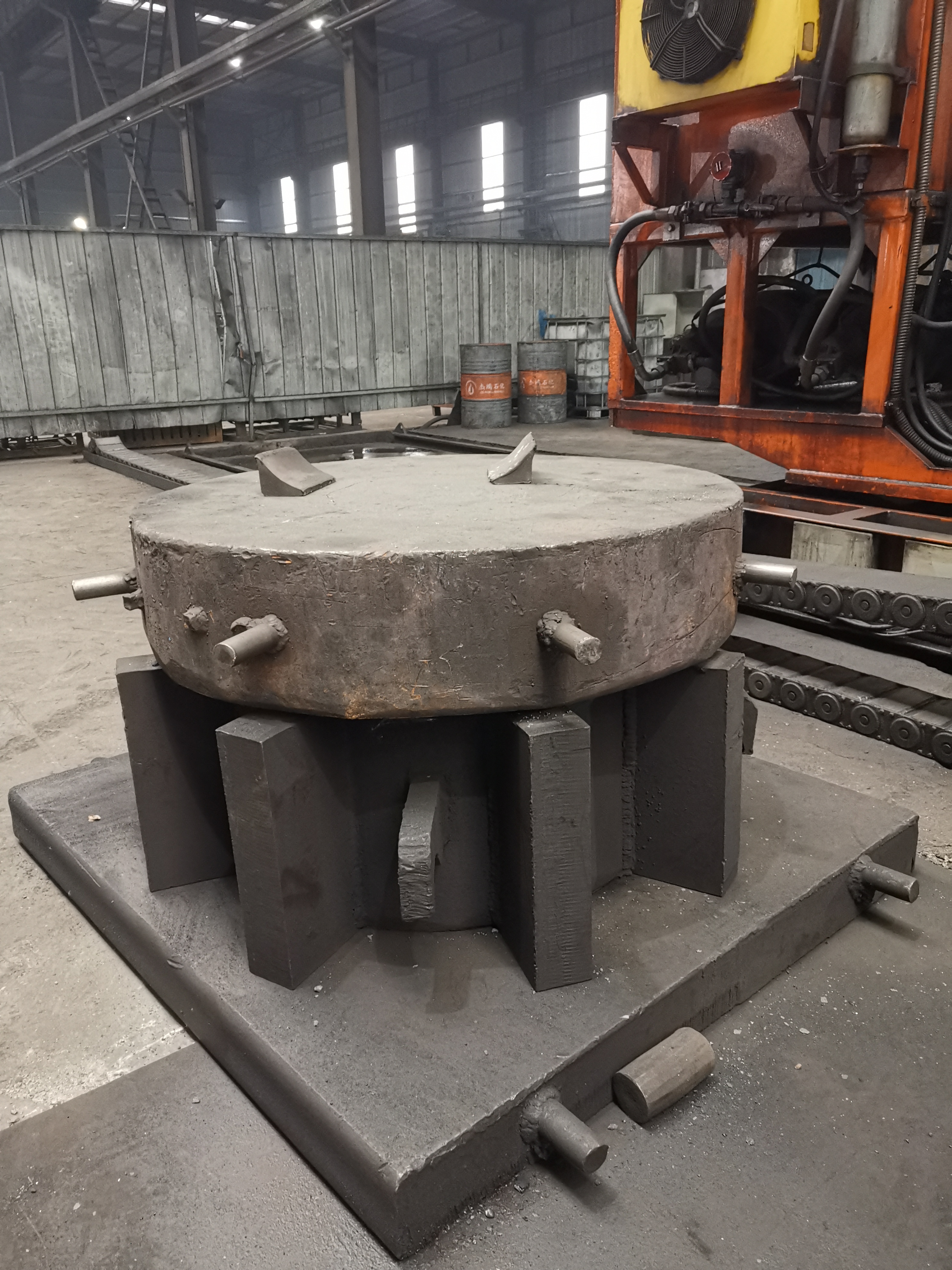