At present, many foreign models have been introduced into Chinese automobile factories and the technical conditions of gear materials have been met with relevant standards. Specific requirements for stable hardenability of H steel (narrow band low carbon alloy carburized steel) has caused widespread attention by steel mills and corresponding departments. It is believed that after a period of time, through the technical transformation of steel mills and the use of good technology, the quality of forging blank gear materials will have a big increase. By then, coupled with the simultaneous adoption of good technology by the automobile industry, the quality of the automobile gear will also have improved greatly.
After isothermal annealing of gear forging blanks (refers to the general alloy carburized steel, for some high alloy carburized steel, isothermal annealing is also difficult to avoid the formation of bainite, need to increase the high temperature tempering process) not only to ensure the excellent cutting performance, but also because it obtains uniform organization, the dimensional stability after carburizing quenching is also of great help. Of course, to make the gear in the process of carburizing quenching deformation is small and stable, but also need the material itself hardenability can be stable, parts placed evenly on the bottom plate to ensure the uniformity of quenching cooling, and the cooling process of the choice of cooling oil, oil temperature, stirring intensity control.
When these blanks are loaded into the furnace, the weight of each part is the same to ensure the same cooling conditions. Through this treatment can avoid strip structure, obtain ferrite - pearlite mixed structure, hardness of 140~170HIB, ensure excellent cutting performance, parts surface finish is good, tool life is longer.
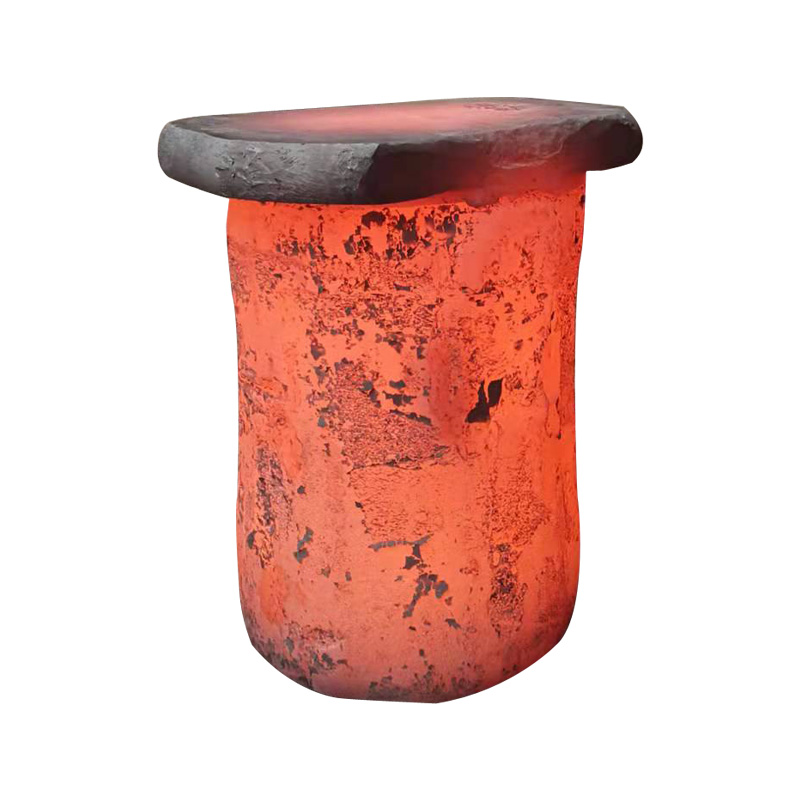