In order to remove the processing stress, adjust the organization, refine the grain, for the subsequent cutting to prepare good conditions, after forging processing to carry out appropriate heat treatment, heat treatment methods including annealing, normalizing, normalizing and tempering, quenching and tempering. In order to ensure the efficiency of heat treatment, most hardness values of the workpiece are specified within a certain hardness range, and a few are specified below a certain hardness value. Brinell hardness tester is used in most of the hardness test methods, while Rockwell hardness tester is used in a few. Individual large workpieces can be used in Shawwell hardness tester or Richter hardness tester.
As we all know, the hardness test of forgings mainly uses Brinell hardness tester, standard or user drawing requirements are also mostly Brinell hardness values, a variety of types of forgings are required to be tested piece by piece, each workpiece also requires the detection of multiple points.
For small forging parts, it can be tested directly on the bench Brinell hardness tester. Large and medium-sized forgings can not be moved to the desktop computer for testing. There are two kinds of hardness testing methods, one is to use portable Brinell hardness tester, the other is to use other portable hardness tester, measured and then converted into Brinell hardness value.
Forgings are generally just blanks of mechanical parts. After the production of forgings, they are sent to mechanical processing plants for cutting. After the cutting, heat treatment should be carried out. Heat treatment methods include normalizing, quenching - tempering, carburizing, nitriding, local high frequency quenching, etc. Some of the workpieces after heat treatment can be used as mechanical parts directly, and some need to be grinding and other final processing, and then used as mechanical parts.
Compared with the mechanical parts processed by other methods (such as extrusion, rolling, casting, etc.), the mechanical parts processed from the blank of forged parts have excellent final resultant properties. These work pieces should have good toughness, but also to reach the specified hardness, with the workpiece in the use of conditions to have the strength, wear, surface hardness or local hardness and other properties. Therefore, after heat treatment of the workpiece to carry out precision hardness testing, the use of hardness tester should be Rockwell hardness tester. Bench Rockwell hardness tester can be used when the workpiece is small. Portable Rockwell hardness tester should be used when the workpiece is large, heavy or long. When portable Rockwell hardness tester is not available or the hardness testing accuracy is not high, the use of a Shaw hardness tester, Richter hardness tester, or hammer Brinell hardness tester.
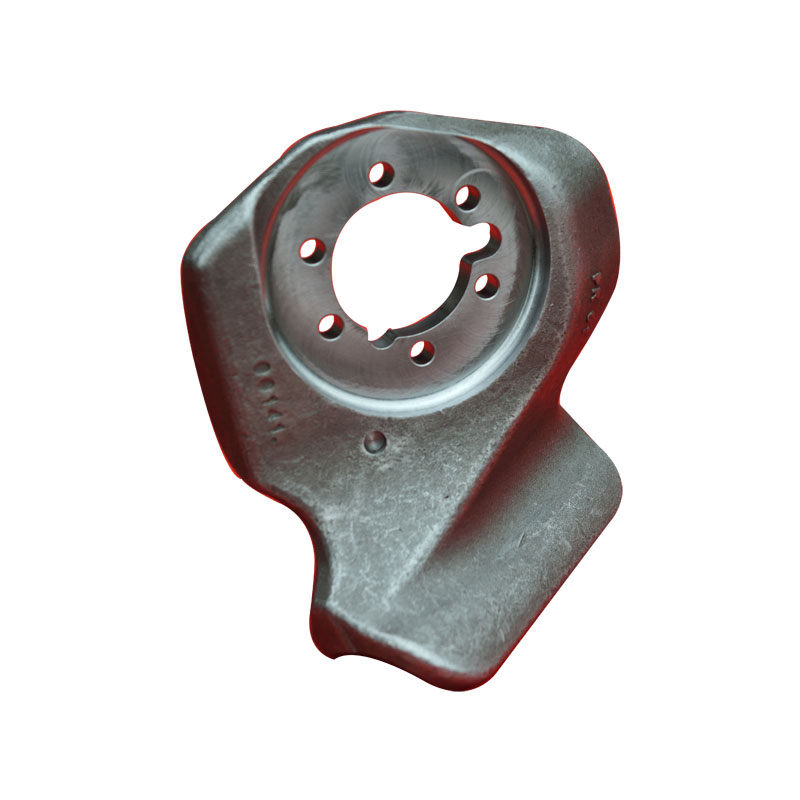