(1) Correctly judge the service time of forgings. The number of times a HSS roll is used between grinding operations depends on the maintenance of the oxide film after each roll and the roughness of the roll surface. Normally, the front of the frame can be used 3-7 times, the back of the frame can be used 2-4 times, and the CPC HSS roller can even be used more than 10 times.
(2) Adopt roll surface flaw detection to avoid roll failure accidents. After the HSS roll leaves the mill, water cooling or air cooling should be carried out in time to ensure that the thermal expansion of the next roll forging is eliminated before use. High speed steel rolls are prone to thermal cracks. In case of abnormal rolling shutdown, the HSS roll needs to be replaced in time. In order to avoid failure accidents such as roll spalling, acoustic flaw detector should be used to detect cracks on the roll surface after cooling.
(3) Use the corresponding tools to improve the grinding results of forging parts. Because of the high hardness of HSS roller, grinding is difficult, special grinding wheel and automatic grinding machine should be used. After grinding, the eddy current flaw detector and ultrasonic flaw detector should be used to carry out composite flaw detection on the roll surface. Under normal operation, HSS rollers can be used on machines with slight thermal cracks after grinding. On the basis of eliminating the surface crack of high speed steel roll under roll accident, it is necessary to increase the grinding amount.
The way the forgings are used and the accumulation of working time, as well as the passivation film on the surface, all suffer varying degrees of damage over time. Therefore, it is necessary to clean and maintain the forging surface regularly to extend the service life. When cleaning non-forged surfaces, be careful of surface scratches, and avoid using bleach and abrasive cleaning solution, wire balls, grinding tools, etc. To remove the cleaning solution, clean the surface with clean water after cleaning.
If there is dust on the surface of the forging and the dirt is easy to remove, it can be cleaned with soap, weak detergent or warm water. Trademarks and films on the forging surface should be washed with warm water and weak detergent, and adhesive components should be scrubbed with alcohol or organic solvents, ether and benzene. If the surface is contaminated with grease, oil and lube, wipe it with a soft cloth and then clean it with a neutral cleaner or ammonia solution or a special cleaner.
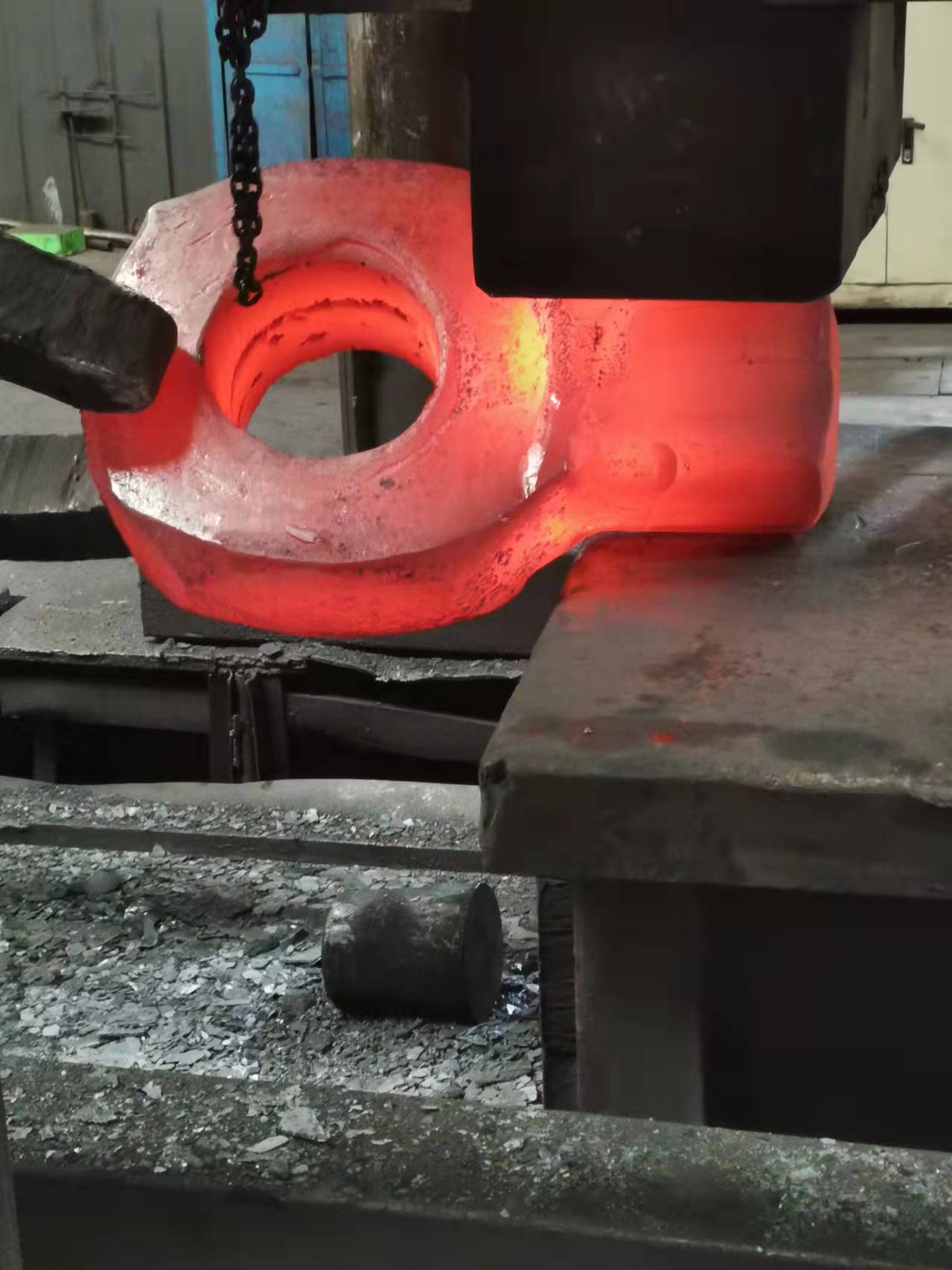