While pursuing high speed machining, it is necessary to shorten the production auxiliary time as much as possible to obtain good technical and economic benefits. The CNC press is equipped with three coordinate loading and unloading device driven by servo motor, which can make the stamping center realize efficient plate processing. Thus several processes or several processes in a machine tool to complete the composite, is the current various types of machine tools greatly reduce the production of auxiliary time, improve productivity important technical approach, in forging machinery has also been successfully applied, the effect is very significant.
Such as: Germany, the United States, Japan has developed laser step blunt composite machine, die cutting and laser cutting organically, a workpiece feeding can complete punching, punching, flanging, shallow drawing, cutting process, utmost ground saves the auxiliary time, is particularly suited to pass multiple and complex machining of panel class and more varieties of small batch sheet metal processing.
Therefore, improving the efficiency of forging processing is the primary task of forging factory, so as to have more productive efficiency.
Now the development of forgings is faster and faster, but also more and more widely used. Production integration is one of the most striking development trends in the production technology of forgings. If forging factory production of forgings, die forgings and other metal products, in the development of manufacturing industry, forging factory production product quality requirements also more and more high, new materials, structure weight, enhance the reliability and durability of the forgings, shorten the manufacturing cycle of equipment and reduce the manufacturing cost has been forging factory production of important ideas. Make the new era of forgings toward the trend of large, integrated, precision development.
The production of forgings factory relies on large forging equipment and advanced die forging process, which complement each other. Equipment is the foundation, technology is the guarantee means. The development trend of large forgings is inevitable, the use of advanced forging equipment to achieve the precision control of the whole process of production of large forgings, to provide large, precision, high life, high performance, low cost forgings, which is also the goal of the development of advanced forging technology.
The materials used in the production of forgings include: alloy steel, carbon steel, aluminum alloy, titanium alloy, high temperature alloy, ultra-high strength steel, stainless steel and so on. The structural form, material properties and quality of the forgings, manufacturing cost is one of the important factors that determine the performance, reliability, life and economy of the forgings.
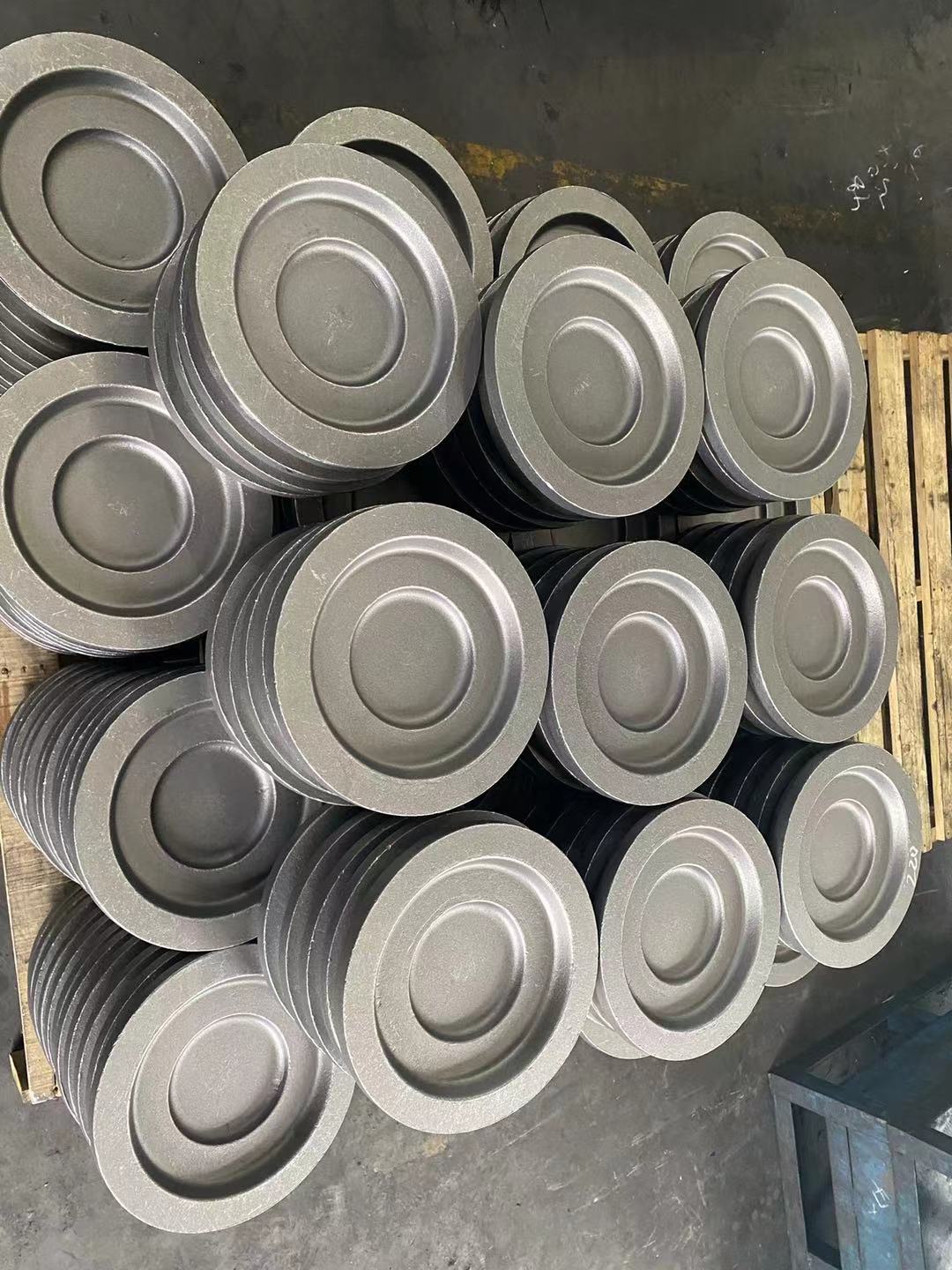