The main process of free forging:
1. Upsetting -- the process of reducing the height of the blank and increasing the cross section area.
2. Elongating -- the process of reducing the cross section of the blank and increasing its length. The drawing process is also known as "stretching"
3. Punching -- the process of forging a through hole or semi-through hole on the blank
4. Reaming method -- the process of reducing the wall thickness of hollow billet and increasing its outer diameter
5. Drawing of mandrel -- the process of reducing the wall thickness of hollow billet and increasing its length
6. Bending -- the process of bending the blank into a specified shape
7, rolling - eliminate the drum shape after the upsetting of the cylindrical blank, so that its shape is more regular auxiliary factory sequence
8. Dislocation -- the auxiliary process of keeping the axis parallel while keeping one part of the blank apart from the other part
9. Torsion -- the auxiliary process of rotating one part of the blank about another part about an axis of another part
10, cutting - cutting billet (cutting) or part of the separation (cutting) auxiliary process
11. Forging joint method: heat two billets to high temperature, and then forging and welding into a process, also known as "closing fire", "cooked fire".
Subsidiary processes of free forging:
Ingot chamfering and neck chamfering, prepressing clamp handle, ladder shaft forging indentation, etc., pre-deformation process before the billet enters the basic process.
Free forging refitting procedure:
Used to refine the size and shape of forgings to meet the required process graphics. There are indentation surface and indentation surface drum roller and cut roller, convex, concave uneven, indentation surface indentation surface, indentation surface after bending rectification, forging oblique correction and other procedures.
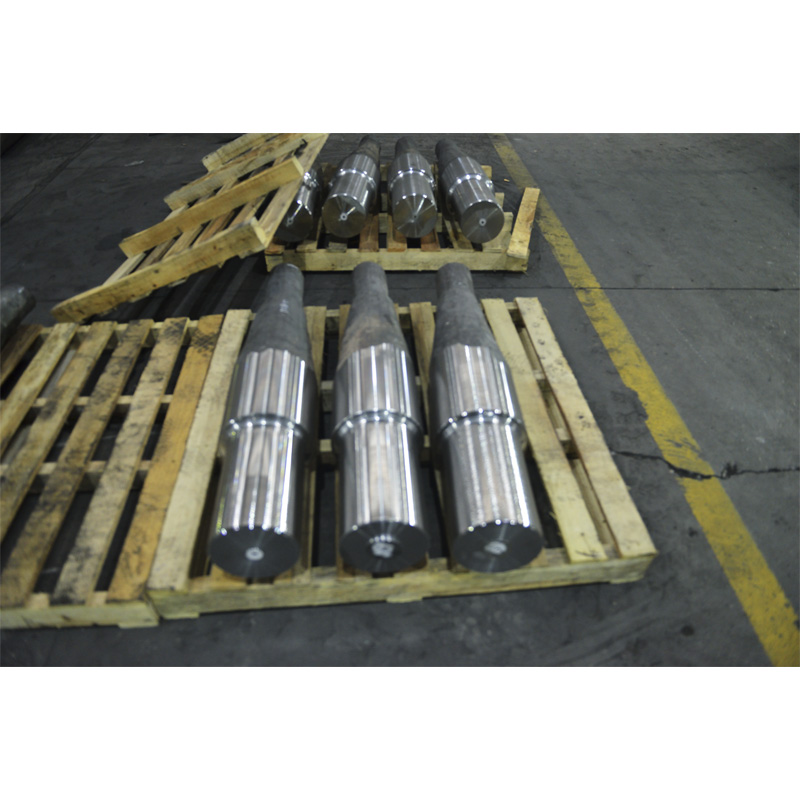